Enjoyable interview last week.
Thanks to Dorota Sokolowska & our friends at 314 Apps in Peterborough, UK.
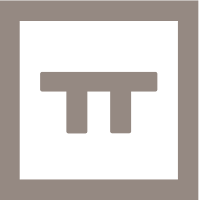
(Fine app development company that's applying Lean fundamentals in interesting ways.)
Here's the transcript.
- Why are Lean principles so important for our business?
Lean, also known as Toyota Production System (TPS) allows us to do more with less – less hassle, less energy, less pollution, less overtime, fewer resources of all kinds – while giving our customers what they want, and reducing human misery. Lean helps provide meaningful work and prosperity, while engaging everybody in the organization in improvement. Lean, thus, builds capability, self-respect & confidence. - In your book Getting the Right Things Done you elaborate upon the concept of Strategy Deployment. How would you explain it?
Strategy Deployment (aka Hoshin Kanri) has been called 'the world's most powerful planning & execution system'. SD is a proven approach to breakthrough performance that aligns everybody toward True North, our strategic & philosophical goal. SD opens up time in everyone's schedule for breakthrough work. But that entails implementing a solid Lean foundation comprising standardized work, visual management and the like.
- How is Strategy Deployment different from other types of planning?
Underlying SD are a set of core 'mental models' – ways of thinking – that are fundamentally different from what we're taught in our business & professional schools. At Toyota manufacturing I had to unlearn everything I learned in engineering school. The biggest obstacle, therefore, is ourselves. We need to deepen and extend our mental models – a difficult but essential prerequisite.
Secondly, SD depends on total participation, which has major implications for how we manage. Respect for people becomes a foundational principle. Employment stability is job one. People won't get involved in improvement work if they don't feel secure. So, we have to commit to employment stability, we have to teach our people Lean basics, and reduce the hassles that hinder improvement work. Everything is connected, as they say. - How are people and companies using your books?
Pleased to say, people are using my books are working tools. They form study groups & book clubs, and work on the questions at the end of each chapter. It's gratifying to see dog-eared copies of my stuff in factories, design studios, and hospitals. When a supervisor pulls out a copy of, say Andy & Me, or The Remedy and asks about a concept, I'm honoured.
Writing is hard, but connecting with people makes it worthwhile. - What is the most important lesson that you learned while working in Toyota?
Respect for people is the foundation of any great enterprise. People have knowledge, capability, and creativity. Everybody has the God-given right to be involved in improving their work and organization.
This doesn't mean Shangri-La, a place where everything is nice and nobody is ever stressed. Sometimes 'respect for people' means challenging your people to go places & do things they don't think are possible. Going easy on people doesn't necessarily entail respect. In fact, it could mean the opposite.
We're on this Earth for a short time. It's our duty to try & get a little better every day, 'to seek, to strive and not to yield'. (Thanks, Lord Tennyson.) - What advice would you give to a newbie businessman?
Learn the fundamentals – Value & Waste, standardized work, visual management and the like. Join a good organization committed to Lean fundamentals, especially respect for people, and learn by doing.
Practice, practice, practice for decade or so (or 10,000 hours according to Malcolm Gladwell). Then start to teach others what you've learned.
Above all, stick with it. Don't be side-tracked by 'shiny objects', the buzz words du jour, and the latest management fads. The fundamentals are forever.
Pascal
No comments:
Post a Comment